Digital application of industrial robots
Now we hear the word IoT. This is mainly about controlling the operation status of machine tools and industrial robots in factories and what is produced with digital data. Yaskawa is promoting the i3-Mechatronics concept.
Industrial robots are good at repeating the same movements over and over again. However, once it’s installed and turned on, it doesn’t mean to work 24 hours a day without stop, and sometimes it unintentionally stops. Even in such cases, YASKAWA Cockpit, a proprietary software program, can be installed to monitor the operation status of 100 types of digital data, including vibration and torque values emitted from servo motors built into the joints of industrial robots. This allows us to monitor the current movements of robots, monitor the tendency for alarms, and investigate the cause of the failure with operation data.
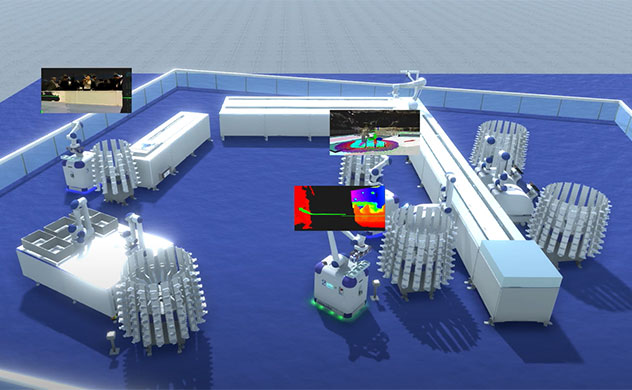
Digital Twin
In the IoT and industrie 4.0 trends, the term “digital twin” has emerged. This allows the production line to be simulated over and over again in the same virtual manner, reducing the time required for robotic system setup and enabling remote control.
In addition, by collecting various data on the operation status of the actual production line and simulating it on the virtual production line, more efficient operation conditions can be found and fed back to the actual production line to maximize the performance of the production line itself. In order to achieve this, it is essential to digitally manage all of the facility’s operational data.
i³-Mechatronics is being developed from both hardware and software perspectives, including the development of a new controller and YASKAWA Cockpit software for digital data management.
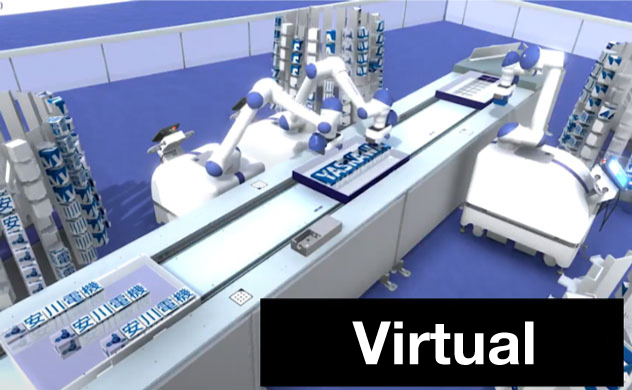
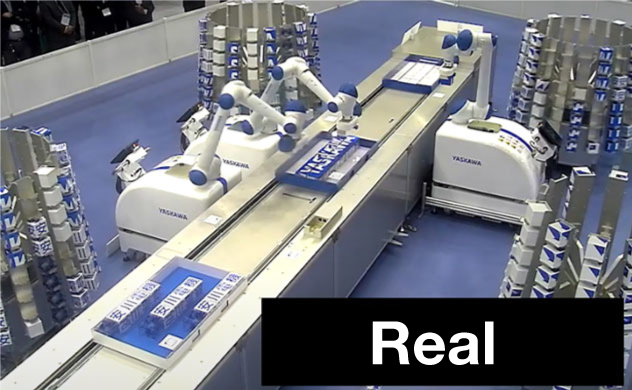