i3-Mechatronics Offers Solutions for Customers’ Smart Factories
The term “”IoT” or “industrie 4.0” has come to be used in a broad meaning in recent years because of advances in telecommunications technologies, and many things such as automobiles, factories, and home appliances are connected digitally. Yaskawa promotes i3-Mechatronics as a solution concept in response to such trends in IoT and industrie 4.0.
At i3-Mechatronics, we propose that in addition to automating “cells,” digital data should be used to manage these tasks. This enables us to manage the operation status of equipment with process data and the production status with status data as “numerical values” rather than “expert knowledge”. We want to provide our customers with data management that eliminates red lights that are out of service and keeps the green lights on at their factories.
Solutions offered by i3-Mechatronics
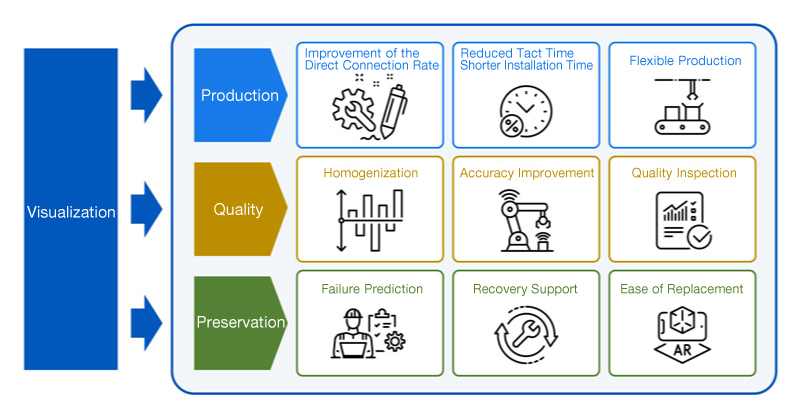
The i3-Mechatronics will proceed in three “i” steps: (1) integrated, (2) intelligent, and (3) innovative. Specifically, we will connect the factory cells and systems such as equipment and devices to the IT layer by (1) integrating data. Next, the collected data is analyzed and fully utilized (2) intelligently. By doing so, we will be able to achieve (3) innovative, such as the improvement of operating facilities and the stability of production quality, and consequently resolve business challenges that customers are seeking to build smart factories.
Let’s look at what you can do with i3-Mechatronics with each solution.

Data Visualization by YCP
First of all, in order to promote smart factories, it is important to visualize the situation in which the equipment/devices of factories such as industrial robots, machine tools, and sensors are integrated and operating in integrated, which is the first i of i3-Mechatronics.
The features of Yaskawa Cockpit (YCP), a software tool for this purpose, are the “collection, accumulation and analysis” of data through visualization. In the area of data collection and accumulation, it is possible to link various equipment and devices at production sites, including those of other companies, to YCP, to collect data in units of one-millionth of a second by combining the time series of each equipment, and to match the time stamp.
For data analysis, YCP enables you to execute analysis models such as inferences, created by AI, on upper-tier. Additional add-ons such as health monitoring and production count monitoring are also added, and IT vendors provide centralized control of the transfer of data to upper-tier systems such as ERP, MES and Big Data.
By introducing YCP, it is possible to perform predictive failure diagnosis, operation status monitoring/diagnosis, equipment abnormality diagnosis, quality defect detection, etc.
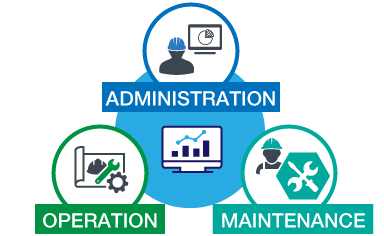
Customizing Data for Each User
From a large amount of data, it is possible to customize the type of data to accommodate users and manage the data efficiently.

Shorter installation time
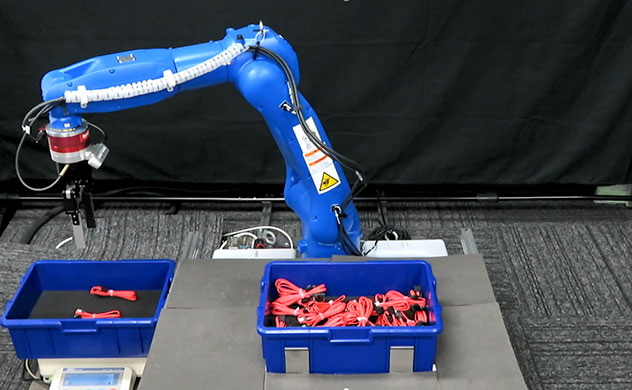
AI Picking
By utilizing the AI technology “Alliom” developed by Yaskawa Group, the installation time to actual operation is drastically shortened, and the accuracy to actual machine can also be improved.
Flexible production
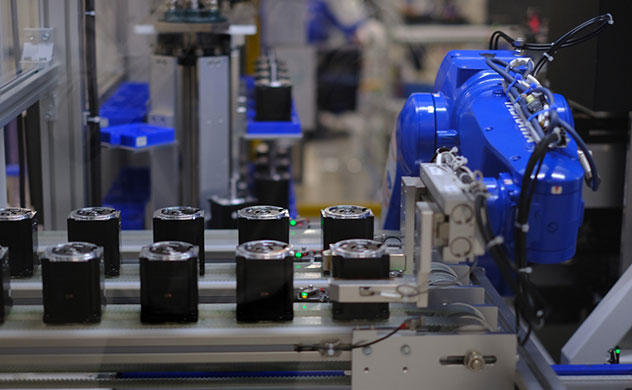
High Variety and Variable Quantity Production
By using digital data to manage automated production lines, setup can be prepared automatically without manual intervention, enabling high variety and variable quantity production from a minimum of one unit.
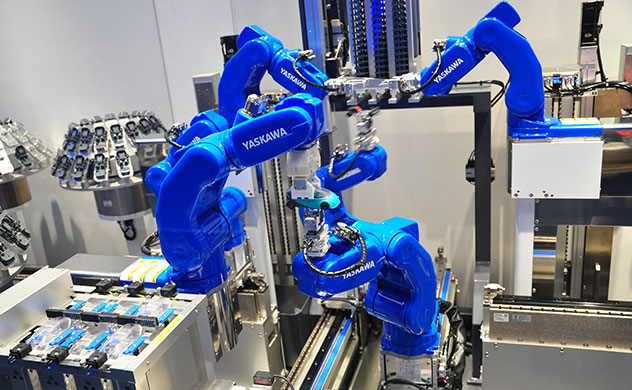
Autonomous Distributed Manufacturing
Digital data such as the torque value, vibration value, and temperature of the servo motor is absorbed into the controller, and the robot can think for itself how to move.
Recovery support
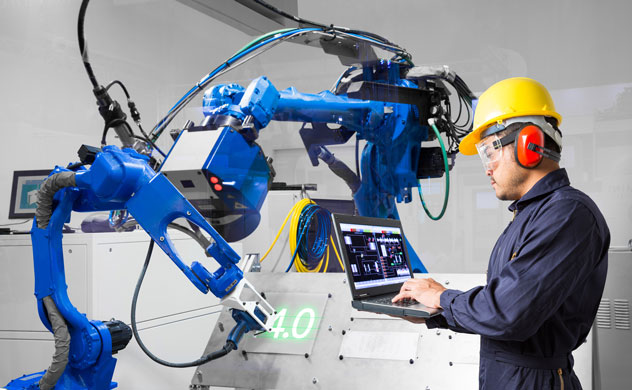
Investigating the Cause of Equipment Failure
By acquiring quality data on when, with which equipment, and how it was processed, it is possible to accurately identify the cause of the problem between which equipment and equipment at the time of failure.
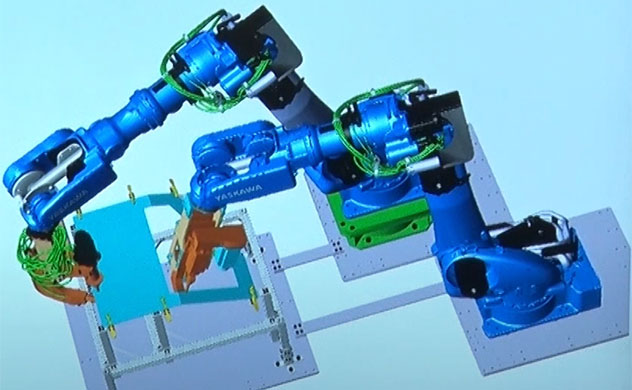
Faster Recovery Simulation
The planning technology that Yaskawa developed automatically generates optimal paths, enabling simulation in a few minutes and dramatically reducing engineering time for recovery from sudden stop.