Birth of Variable Speed Motor Drives and AC Drives (inverters)
Variable-speed motor drives in recent years are centered on the speed control technology of AC motors such as induction motors and synchronous motors. But in fact, DC motors have been widely used for a long time as a representative of variable speed drives because of the ease of speed control. While at the same time, DC motors requires a regular maintenance as well as replacement of brushes because of commutators and wear parts, and there was an issue that it was unable to apply in adverse environments such as dusty locations. Therefore, the technical development that can make speed control of AC motors as easy as DC motors was expected.
In 1958, GE of the U.S. developed a semiconductor device thyristor with control capability, and it opened the path of variable speed drive of an induction motor by an AC Drive (inverter). “AC Drive (or inverter)” means “inverse transformation”. The AC Drive or inverter devices can control the number of rotations, that is the speed of the AC motor by converting AC (three-phase or single phase) once into DC, and converting this DC into again “three-phase AC whose frequency can be flexibly changed”. In order to convert direct current to alternating current, we use semiconductor device thyristor that can perform this switching.
The Limitation of Thyristor
The technical development of Yaskawa’s AC drive (inverter) dates back to the 1960s. At that time, the slow response thyristor was used for the AC drives (inverters). The control technology is also mainly based on V / f control of an induction motor which controls to make the ratio of voltage and frequency applied to the induction motor constant, and the speed control range is about 1:10 or less, the response is not so fast, and simple variable speed was applied to applications with relatively low load fluctuations. A controllable DC motor was used in applications where high-speed, dynamic control was required. Thyristors have had limitations in their efforts to popularize AC drives (inverters) in various applications.
World’s First Transistor Inverter
Under these circumstances, Yaskawa worked on the development of AC drive (inverter) which uses power transistors capable of high-speed switching in collaboration with semiconductor manufacturers. Overcoming years of trial and error and many difficulties, Yaskawa succeeded in developing a high-speed motor drive for machine tools, and it achieved the commercialization of the world’s first PWM-controlled transistor inverter (VS-616T) in 1974. Since then, it has commercialized various transistor inverters and began to lead the technological development of inverters (AC drives).
However, the V / f system was adopted as the control system at that time, and it was not ideal in terms of speed control range and speed control accuracy. It has decided to develop vector control in order to make a robust structured induction motor have the same control characteristics as a DC motor.
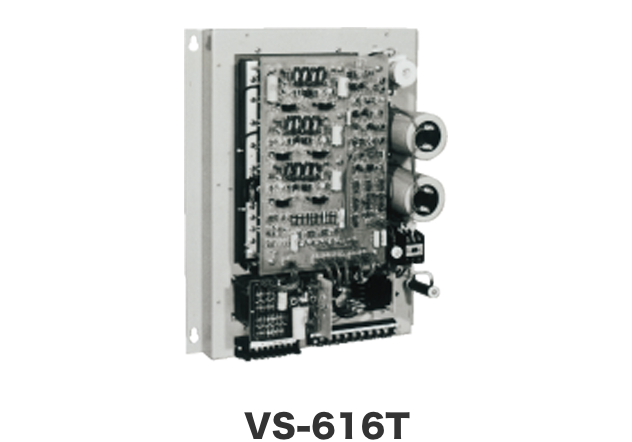
Birth of Vector Control
In the early 1970’s, SIEMENS announced magnetic field orientation control and theory that the induction motor could be controlled in the same way as a DC motor. Yaskawa’s young engineers were aware of the magnetic field orientation control in the article of the technical magazine. They immediately ordered the paper and took a step towards realizing the theory. At that time, high-speed, high-power transistors were beginning to be put to practical use, and the application of instantaneous current control by PWM, which had been developed in advance, made it possible to realize the theory.
However, since there were no high-performance multiplication and division devices, such as vector analyzers and vector rotators, which are necessary for vector control operations, the circuit was finally designed thanks to using thousands of individual parts. As a result of these efforts, it was confirmed that theoretical performance was exhibited, and Yaskawa received the Ohm Technology Award for the unique invention of practical slip frequency control type vector control that does not require a magnetic flux sensor. With this invention, it has created vector control in which the induction motor moves quickly as commanded like a direct current motor.
Applied to Vector Control
The first case to apply for the vector control drive took place in the continuous casting facility of a steel mill in 1978. There were a lot of harmful gas and dust, and the ambient temperature was as high as 100 ° C, which was not the environment where the DC motor can be used. In environments where a wide speed control range of 1:40 is required, V / f control of an induction motor was not feasible. This was made possible by vector control, and the first “Varispeed-626TV” was launched with the speed detector and the features of the induction motor and the vector control performance. The application of this vector control drive has been further expanded, and the world’s first full-AC capable, maintenance-free continuous casting facility has been realized, and nearly 100 rolls are still working in the field. Since then, due to environmental resistance, etc., sensorless control that does not require a speed detector is now widespread.
Growth in Response to the Market Needs
The induction motor drive by the AC drive (inverter) was initially simple variable speed control, but when the high performance drive is put into practical use by the application of the vector control, the torque control was capable and it led to the replacement of the DC motor drive. Furthermore, it realized miniaturization, high performance, multiple functions, and high reliability through advances in digital circuit, power transistors and power conversion technologies. In recent days, a synchronous motor drivehttp://wwwe-mechatronics.com with a built-in permanent magnet has also been commercialized, and AC drives (inverters) representing power electronic devices have been integrated with various control technologies and have been developed in response to many market needs.
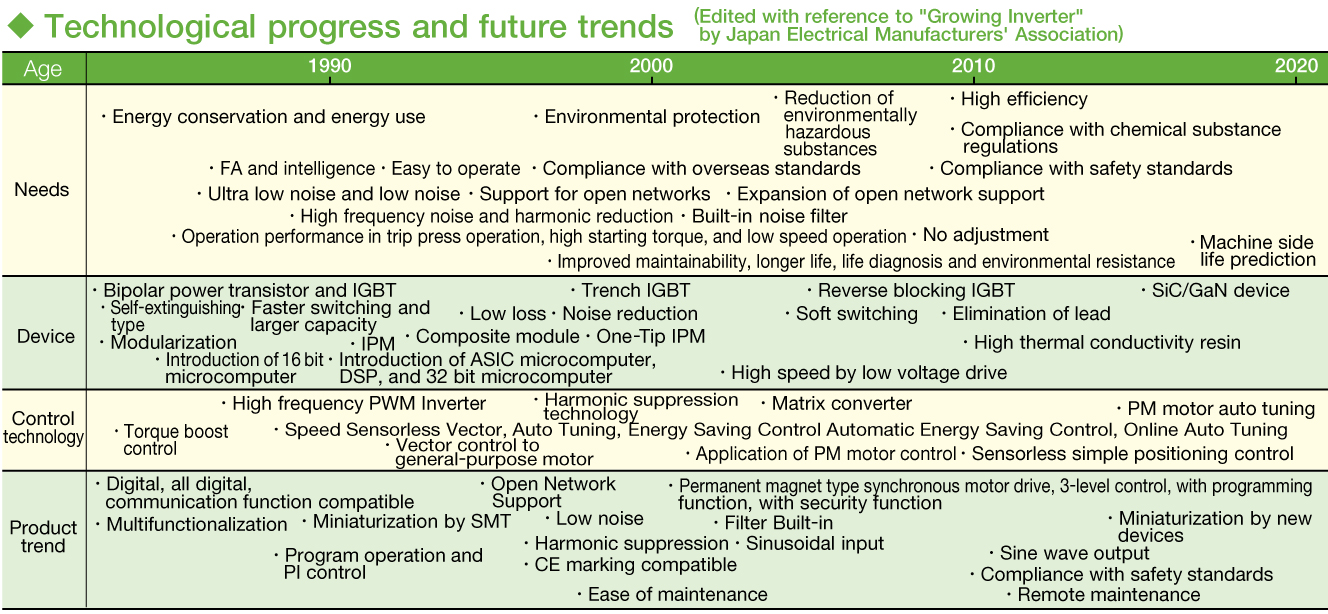