Automobile and Automobile parts
Industrial robots have more than 40 years of history to be used in the automobile industry. Yaskawa still accounts for more than 50% of the applications of industrial robots to today, and robots are used in all processes, including welding, assembly and painting.
For example, robotic applications for arc welding are used for the underside of automobile bodies, mufflers, and seat frames, robotic applications for spot welding are used for joining body sides and ceilings, robotic applications for painting are used for painting, and robotic applications for handling are used for installing seats and windows. Especially in the main line of an automobile factory, the scene of robotic applications for spot welding surround the body and weld it all at once is impressive.
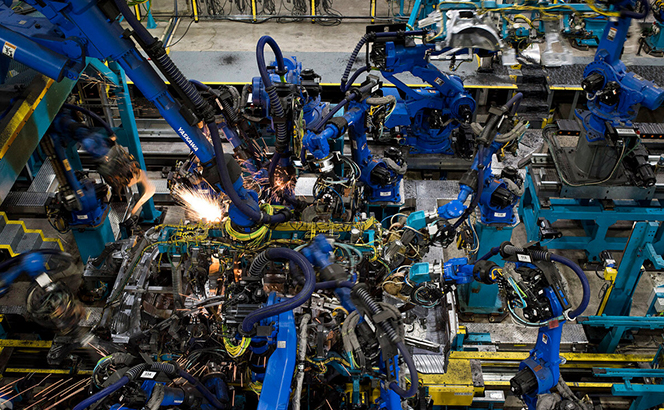
In recent years, electric vehicles (EVs), hybrid electric vehicles (HEV), and fuel cell vehicles (FCV) have become widespread, as environmental regulations have been tightened, mainly in Europe and the United States, and as awareness of Eco has increased. In order to achieve these low fuel consumption performances, the body material has been shifted from steel to aluminum or high-tensile steel sheets that are lightweight and highly functional. New robotics technologies are also required to produce high-capacity batteries, and Yaskawa is developing new products and applications to meet these technological trends.
Electrical and Electronic Equipment
Electrical and electronic equipment is also called “3C,” which stands for Communication, Computer and Consumer Electronics. Industrial robots are also used in various processes to produce electrical and electronic equipment.
For example, mounting small electronic components on an electronic circuit board, welding and painting a casing to store the equipment, and mounting boards and components on the casing. Industrial robots play an active role in almost all processes, from upstream production to downstream testing and shipping, such as testing finished products, and packing packed products into boxes and pallets.
Many electric and electronic equipment products are small, and the production process is closely spaced, making it difficult to apply conventional industrial robots. However, with the appearance of the collaborative robot, which can work with/beside people, these problems have been overcome and the range of applications is expanding.
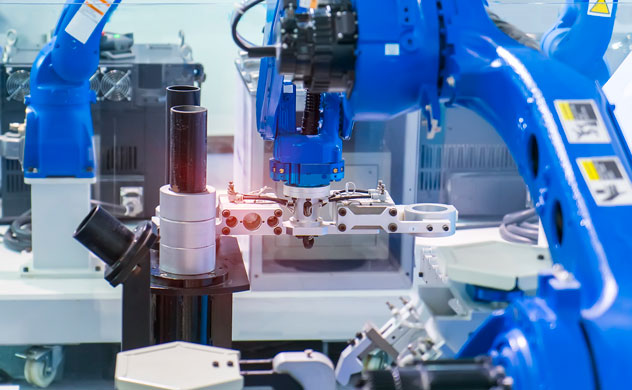
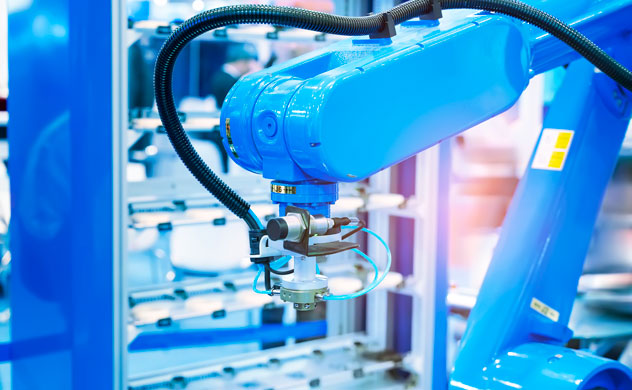
FPD (Flat Panel Display)/Semiconductor Manufacturing Equipment
Thin glass plates (glass substrates) for FPDs is used for PCs, smartphones, and flat-screen TVs. Various processes are used to print patterns and filters on the glass substrate. During this process, industrial robots are used to transport glass substrates and to take them in and out of processing equipment.
In the FPD manufacturing process, a large glass substrate (about a few millimeters thick, and more than 3 meters x 3 meters for large FPDs) is used. For this reason, there is a need for robots that can transport such heavy and deflective glass substrates at high speeds. In addition, even a very small amount of dust and dirt can directly affect the quality, so the factory environment is very clean, and the robot itself is required to have a high level of cleanliness that does not emit a small amount of dust and dirt.
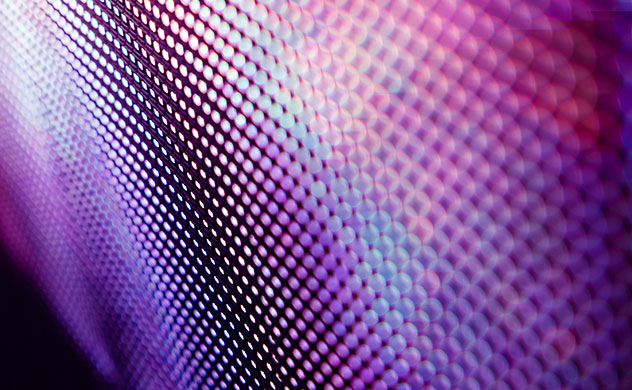
In the semiconductor manufacturing process, thin disk-shaped silicon wafers made from high-purity silicon single crystals are processed. A semiconductor chip called a die is formed by repeating the processes of forming a thin film layer on the silicon wafer, transferring the circuit pattern, etching, cleaning, and inspection. Hundreds of dies are formed on a single silicon wafer. The dies on the silicon wafer are then cut one by one, packaged, and finally inspected.
One of the robotic usage is to transport silicon wafers into and out of manufacturing equipment for each of these processes. As a matter of course, the faster the transfer is, the more it can be produced and the lower the cost. However, semiconductor manufacturing requires extremely high accuracy, and therefore, it has high performance with high absolute position accuracy of 0.05 mm. In addition, as in the FPD manufacturing process, dust and dust directly affect the quality of products, so the factory is kept very clean.
Biomedical
At laboratories and pharmaceutical sites, there are processes such as analysis and quality testing. However, automation was slow because many types of equipment are used, workers are required skills, and there were no industrial robots that could be used under hygiene control.
In response, Yaskawa has developed robotic applications for biomedical field that can move with high precision under hygiene control. We are expanding the range of automation in such fields as pretreatment of experiments and analyses, preparation of anticancer drugs, as well as testing of various types of bacteria. In the case of the preparation of reagents before testing, if the simple work of pretreatment is replaced by an industrial robot and no human work is required, researchers can concentrate on the principal work itself and its efficiency is greatly improved. Safety can be ensured by avoiding dangerous drugs such as anticancer drugs. In addition to this, iPS cells are being cultivated, preprocessed for genome analysis, and tested for the presence of microorganisms.
Industrial robot bodies have smooth surfaces that can be wiped with hydrogen peroxide water and cleaned, and Yaskawa has prepared several models that can work with both robotic arms like a human, and single-arm models.

Food
A food factory usually has various processes, such as packaging, labeling, inspection, packaging in cardboard boxes for shipping, and loading in cardboard boxes, in addition to the production of food products. In particular, the robot is required to have special specifications in the process of processing the food itself in order to handle things that go directly into the mouth. For example, it uses a surface coating that is easy to clean and keeps hygienic, and materials for food machines that are harmless even when put into the mouth. In addition, drip-proof and rust-proof measures may be required in environments where water splashes.
For example, in a factory that produces a large amount of plate-shaped chocolate, a large amount of chocolate is transported to a conveyor in a disassembled state at high speed. Therefore, a robot capable of detecting chocolate on a conveyor with a camera and accurately grasping the moving chocolate is required. For this purpose, a unique structure called parallel link is adopted.
In recent years, as the market for ready-made meals has expanded, some supermarkets and convenience stores have begun to use ready-made lunch boxes and side dishes for filling and closing lids. Collaborative robots can carry trays next to workers and can be installed in limited spaces where safety fences cannot be set up. These robots are expected to be widely used in the future.
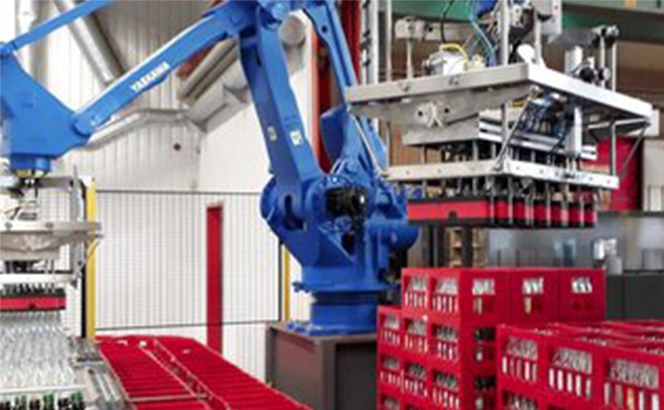
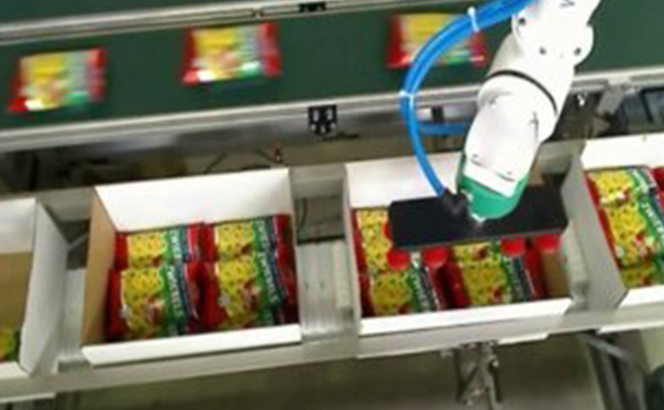
Logistics
As online shopping, such as e-commerce sites, has become increasingly popular, there has been a rapid increase in demand for robotic applications for handling and transporting cartons in distribution warehouses and food warehouses. As the work of stacking cardboard boxes and unloading stacked cardboard boxes is limited, we have developed a special structure model. It is also required that logistics warehouses quickly sort large quantities of packages of different sizes. To this end, we are working with our partners to develop robotics technology for controllers that use CAD-based software to instantly judge their sizes.
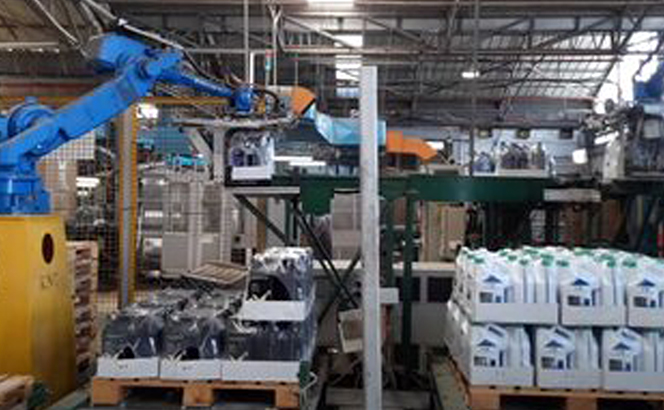